At Renotronic, our repair process is designed to ensure fast, reliable, and high-quality service for all types of electronics. From the pre-assessment to final packaging, every step is carried out with precision. Here’s an overview of how we approach each repair:
1. Pre-Assessment
As a first step we receive the unit, analyze the fault and assess the project based on our former experience. After the assessment, we provide a detailed offer to the client. By making this process, we make sure thar you know exactly what to expect before any work begins.
2. Component Sourcing
Once the offer is accepted, we move into the component sourcing phase. With an inventory of typical spare parts, we can quickly source the components necessary for your repair. As for the more specialized or obsolete components, we can usually source everything, regardless of age, manufacturer or system.
3. Repair or Refurbishment
Depending on your agreement, we either repair or refurbish the unit.. Then the unit is tested if possible.
4. Report & Packaging
The unit is then securely packaged in ESD-safe packaging to ensure maximum protection during shipment. The product is shipped with complete documentation covering the repair.
At Renotronic, we take great care in handling your equipment. Our technicians and electronics lab follow strict ESD standards to ensure maximum protection of client equipment.
Whether you need a quick repair or a complete refurbishment, Renotronic guarantees professional, sustainable solutions that save both time and money.
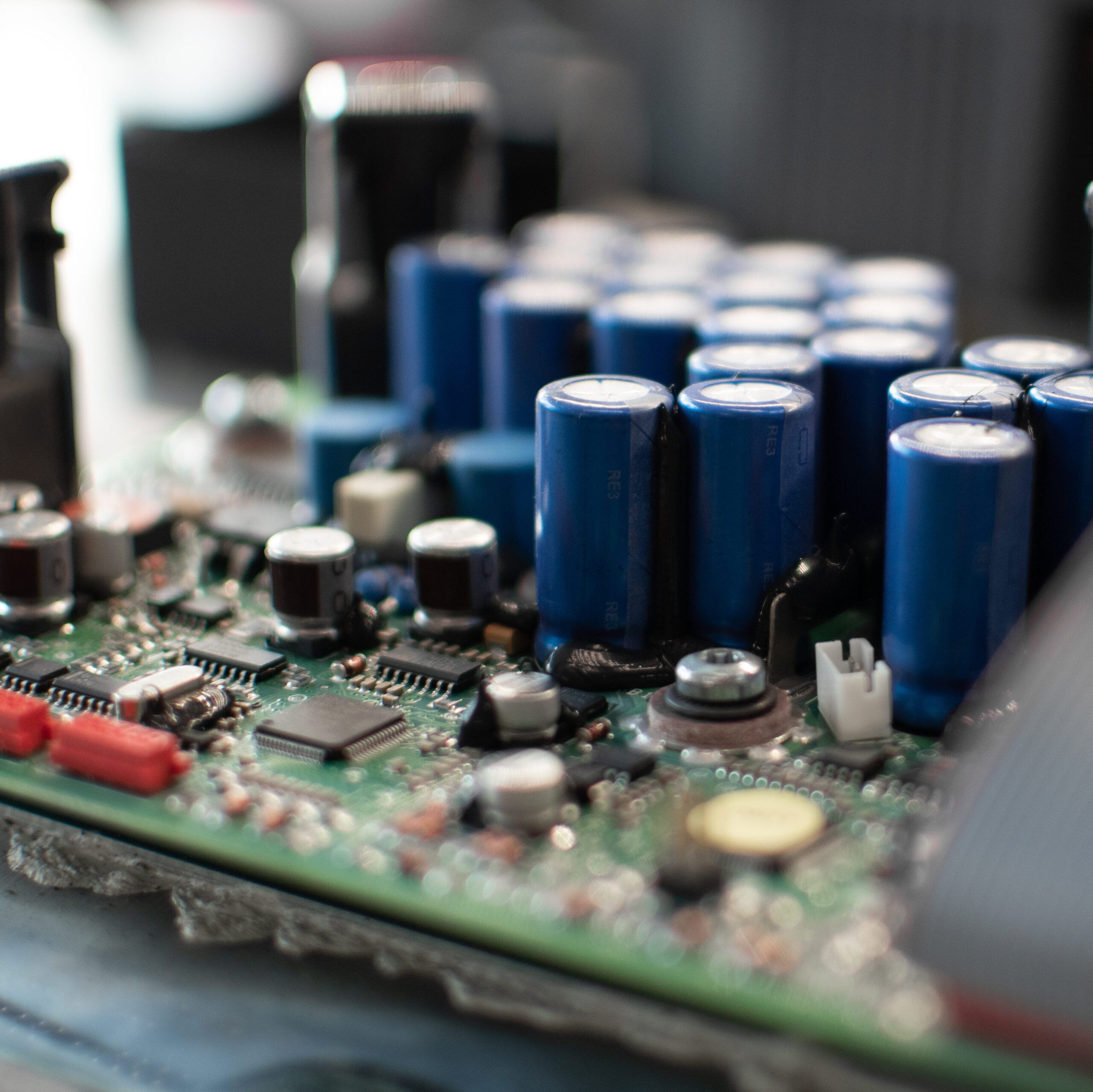
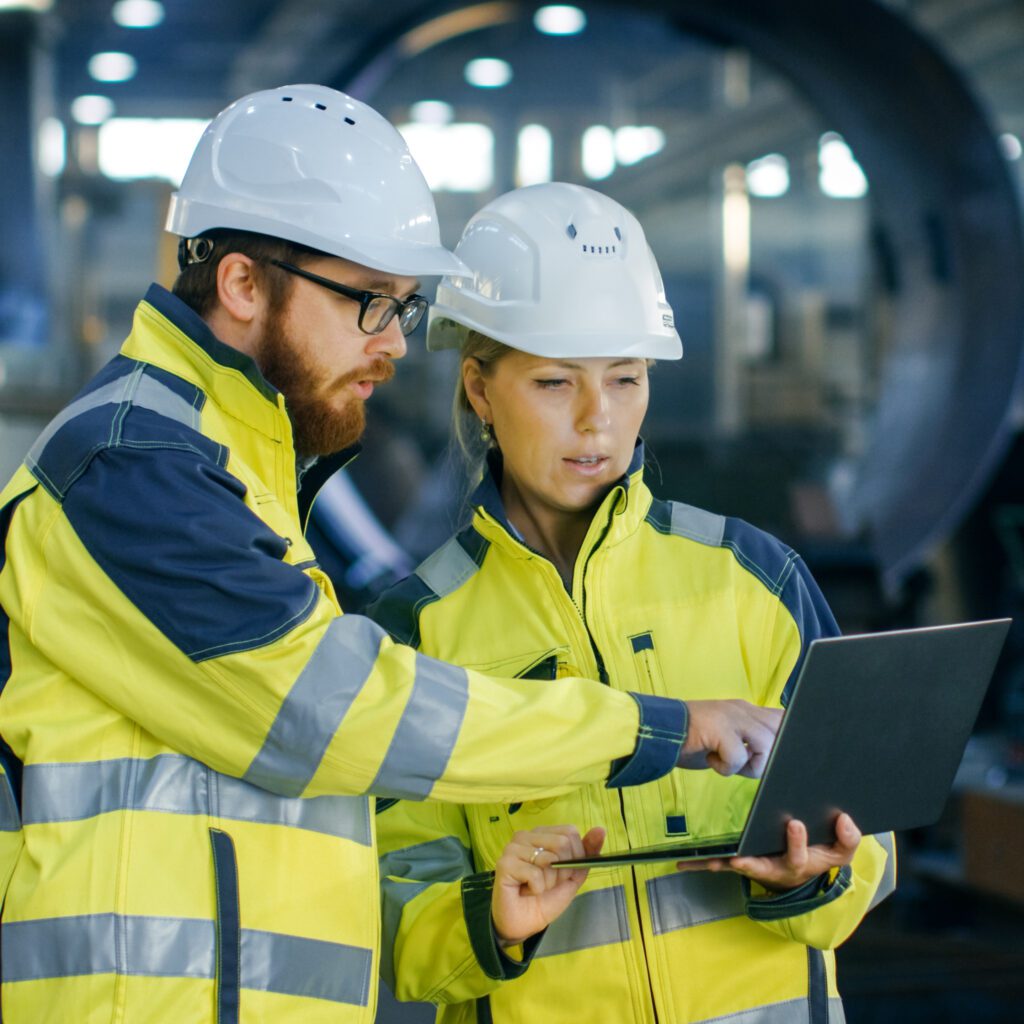
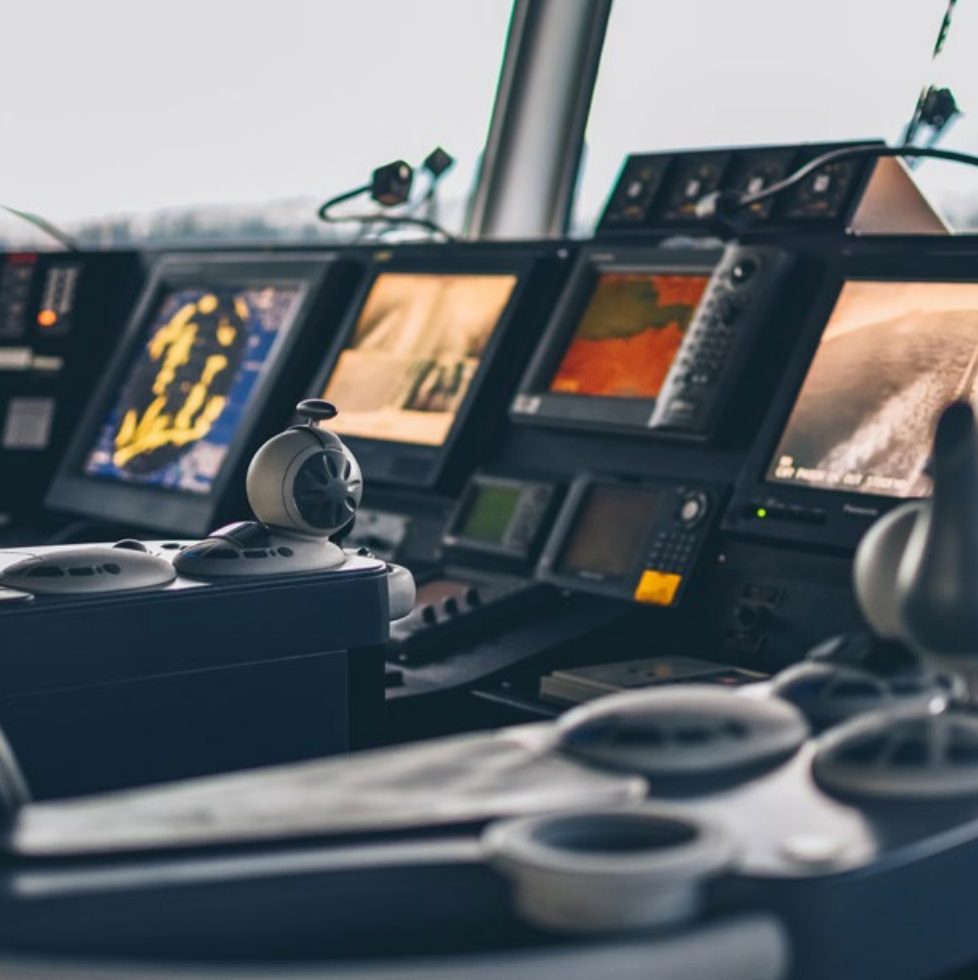